本記事ではCogniteが共催したイベントIgnite Japan 2021のセッションの中から、Cogniteのユーザーである旭化成のデジタル共創本部スマートファクトリー推進センター長である原田様のご講演の内容を紹介いたします。
旭化成の製造現場では実際にはどのようにデジタル化を進めているのか?そしてデジタル化の推進ポイントはどこにあるのか?Cognite製品の活用事例も含めて、本記事で講演の内容をもとにご紹介します。
旭化成が注力している取り組みとその中でのデジタルの立ち位置は?
まず、旭化成ではグループ全体で注力する取り組みを「GDP」と定め、推進しています。
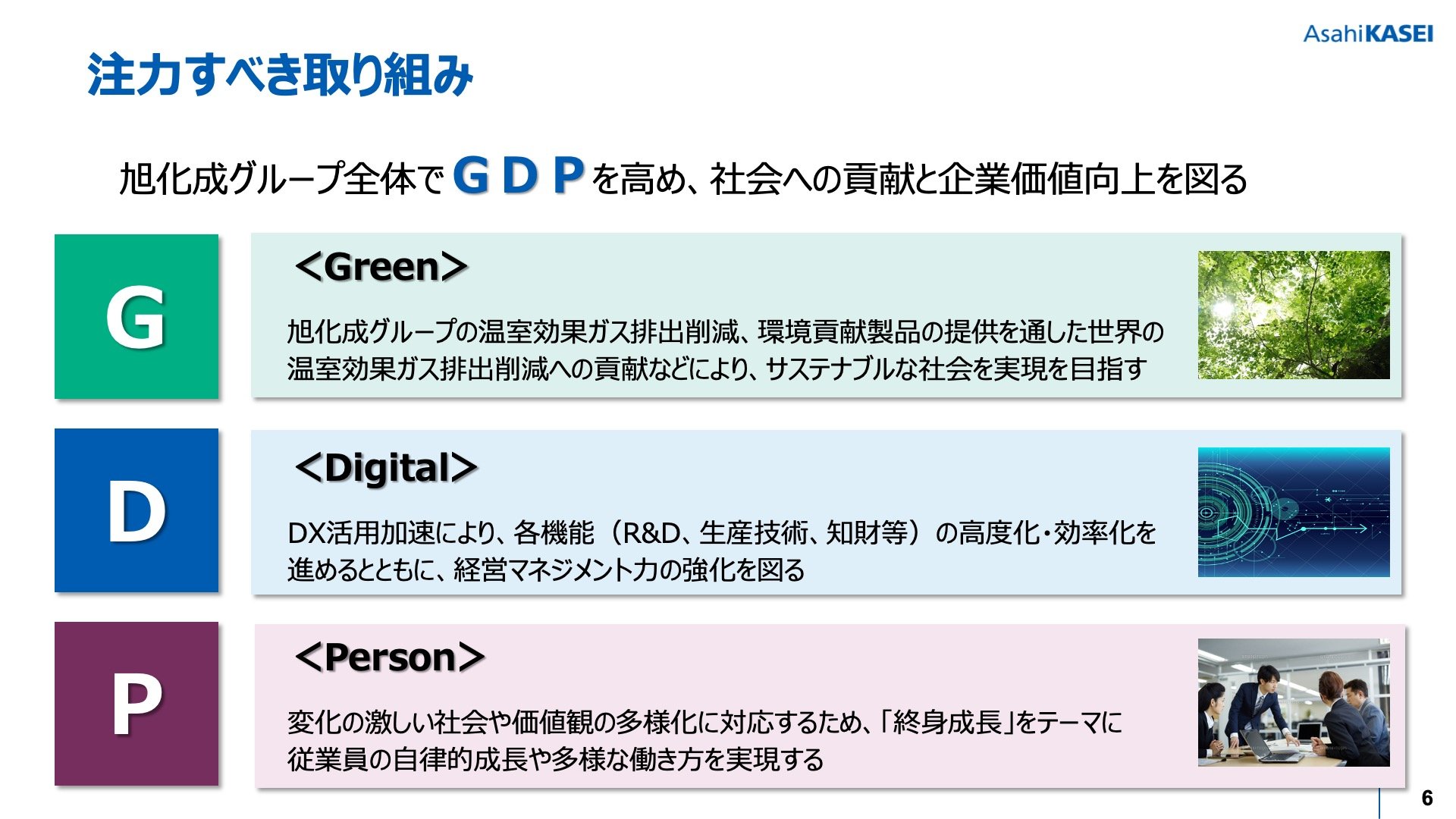
「GDP」の中で、Greenにおいては、環境貢献製品の開発や温室効果ガスの排出量削減を通してサステナブルな社会の実現を、そして、Personにおいては、変化の激しい社会に対応し続けるために、「終身成長」をテーマに従業員の自律的成長や多様な働き方の実現を目指しています。
その中で、2つ目の注力すべき取り組みである、Digitalは、製品開発や人材の育成という事業の中核を成す役割の中で欠かせないものという立て付けになっています。
旭化成の考えるDXのステップと人材の育成プログラム
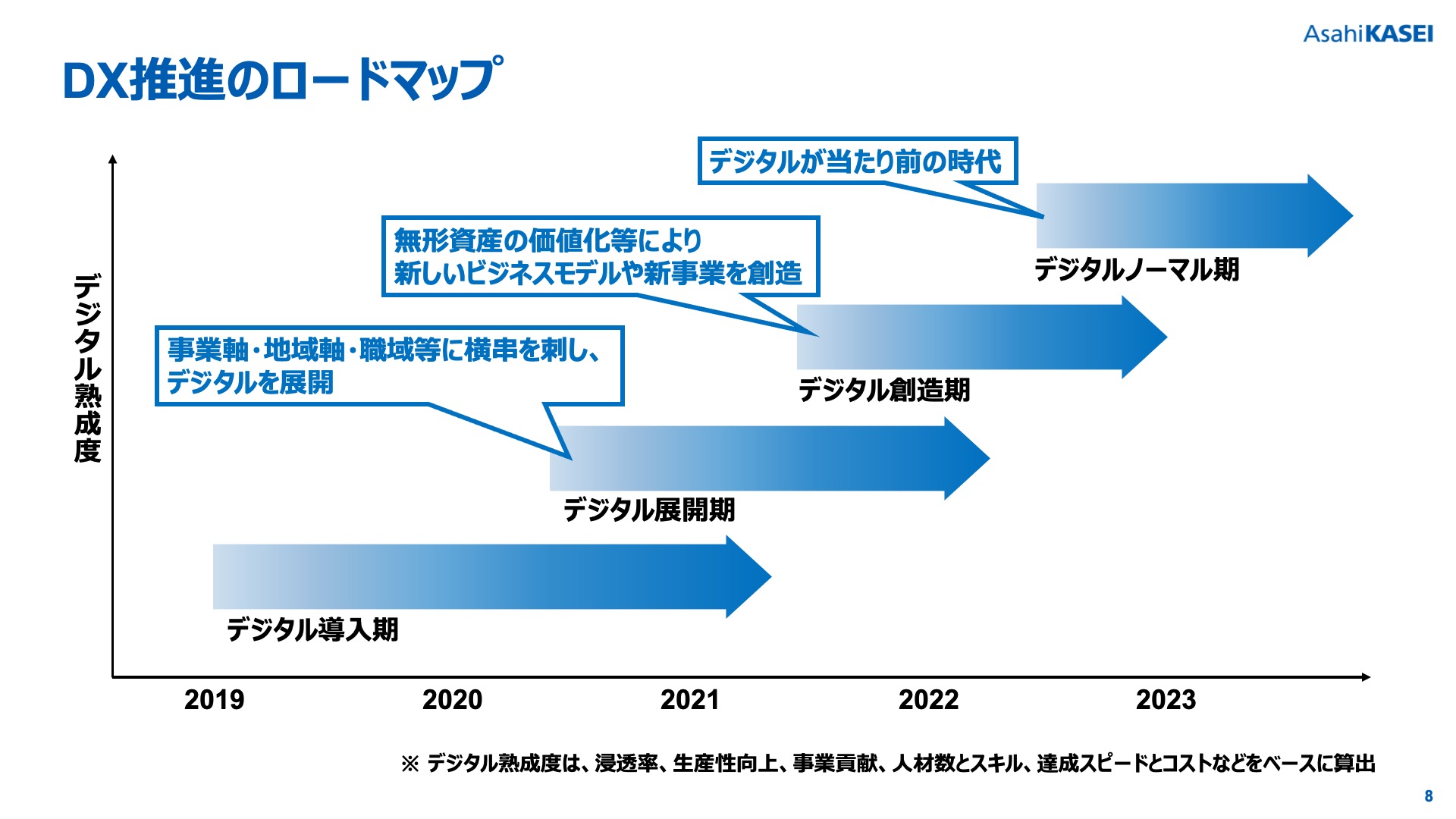
講演では、DX推進のロードマップを下記の年度別達成目標に分けてご説明いただきました。
- デジタル導入期
- デジタル展開期
- デジタル創造期
- デジタルノーマル期
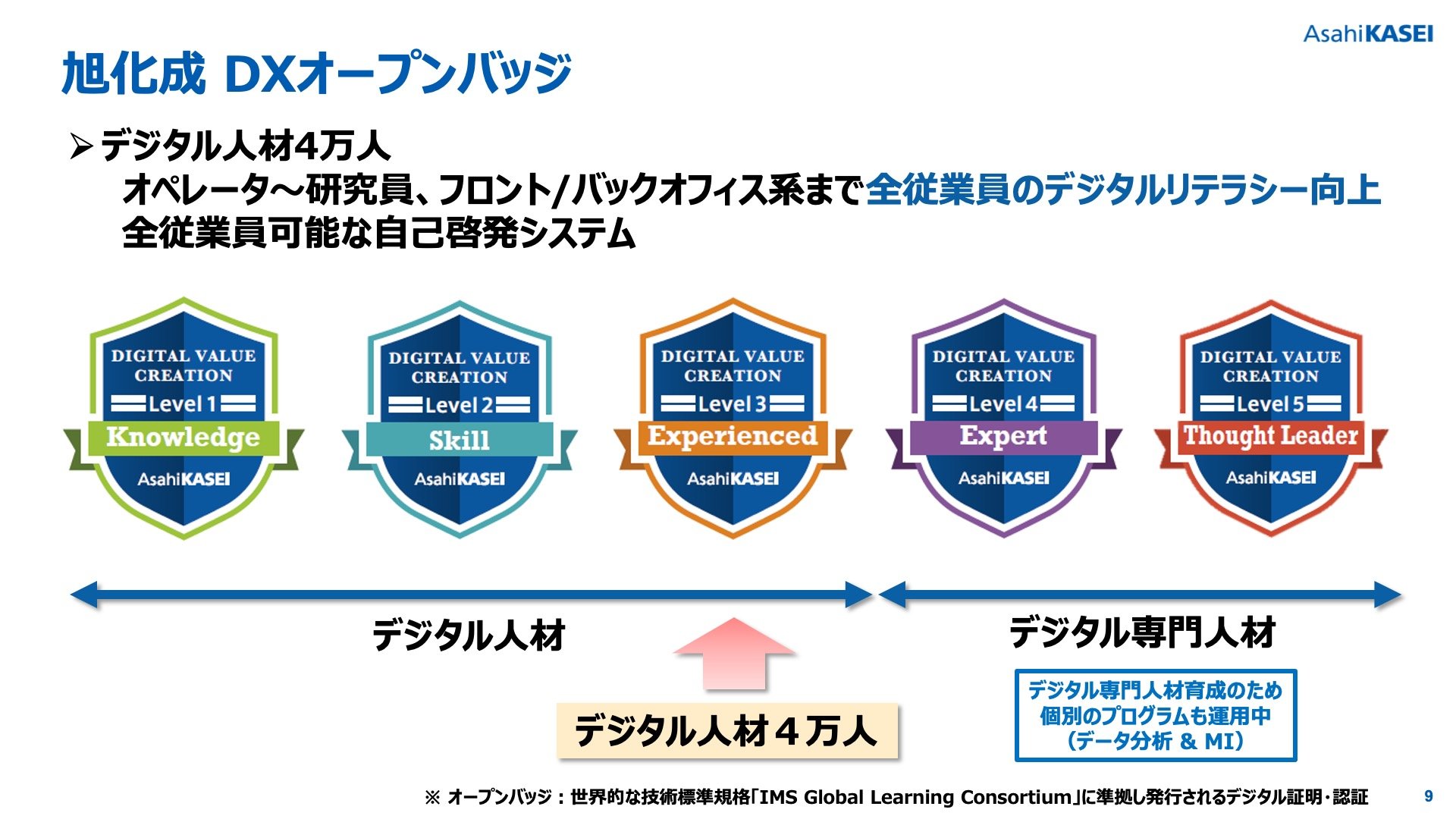
旭化成では、DX推進のロードマップを達成するために社員全員をデジタル人材へと育成するプログラムがレベル別に構築されています。レベル4・5のデジタル専門人材以外でも、業務の専門家などがデジタル技術を活用できるように、すべての社員がレベル3までの育成を目指しています。
旭化成における生産現場の課題と対策
デジタル技術の活用を進めている旭化成ですが、彼らにも生産現場で直面している課題があります。大きく下記の2つです。
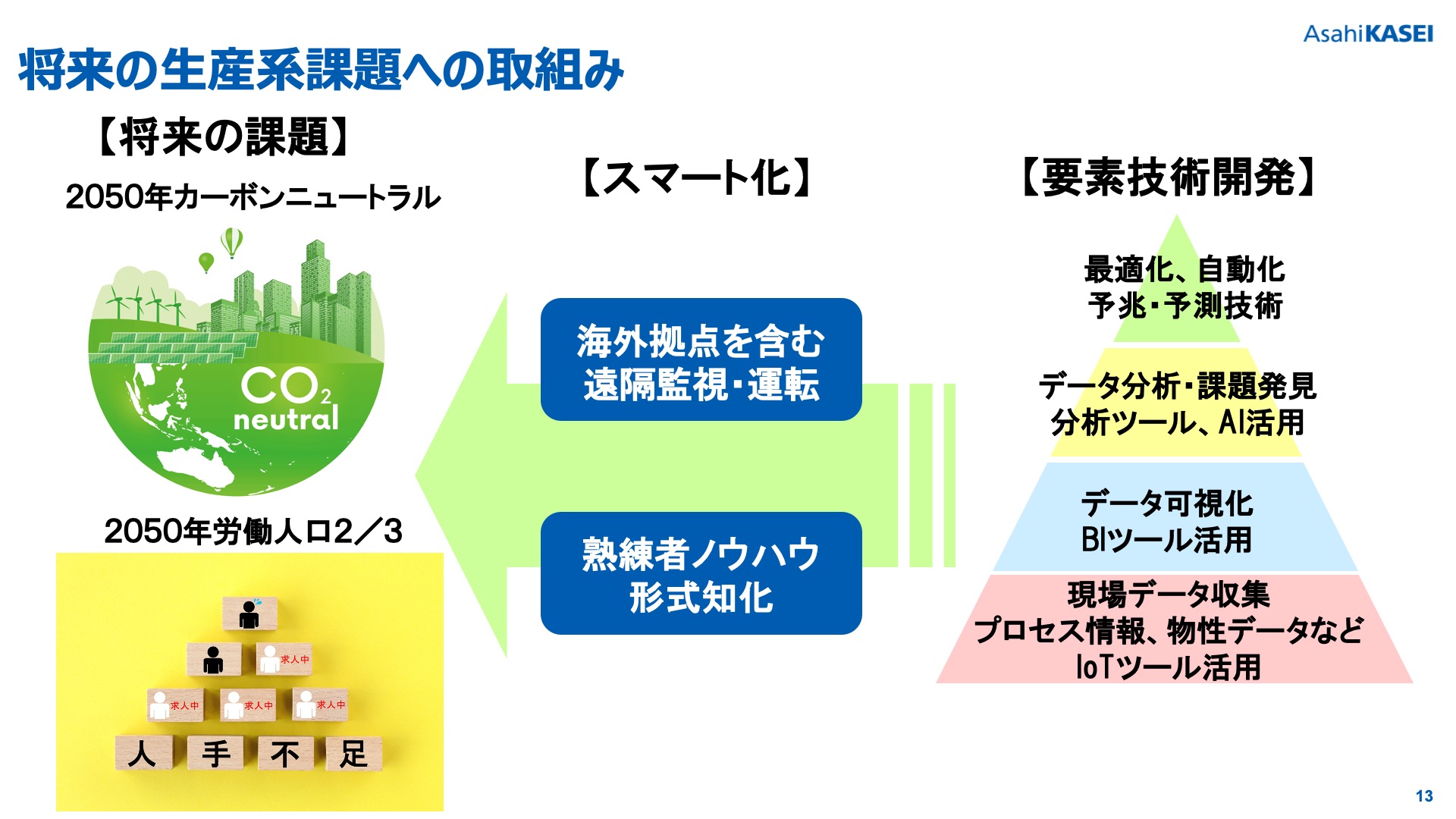
- 2050年のカーボンニュートラルの達成
- 2050年日本の労働者人口が3分の2に減少
旭化成では、これら2つの課題に対して、デジタル技術を活用して海外拠点の遠隔監視や遠隔運転を実現すること、熟練者のプラント運転ノウハウを形式化する(≠ AI化)ことで対策しようとしています。
そして、その対策を実現するため、デジタル技術を4つのステップで活用しています。
- 現場データの収集
プラントの運転ノウハウの原理原則を把握するため、IoTツールなどを活用しながらデータの収集を行う - データの可視化
1で収集したデータをBIツールなどを活用して可視化し、物理現象の理解と課題の仮説をたてる - データ分析と課題発見
2にてたてた仮説を基に、データの分析を行い、課題の発見を行う必要に応じてこのフェーズからAIを利用する - プロセスの最適化と自動化
3にて分析した結果を反映し、プロセスの最適化や自動化を行うこれにより予兆や予測技術の現場適用を実現
旭化成におけるデジタル活用事例
では、実際に旭化成の生産現場ではどのようにデジタル技術を活用しているのでしょうか?
本講演では、スマートグラスを活用した現場力強化の事例をご紹介いただきました。
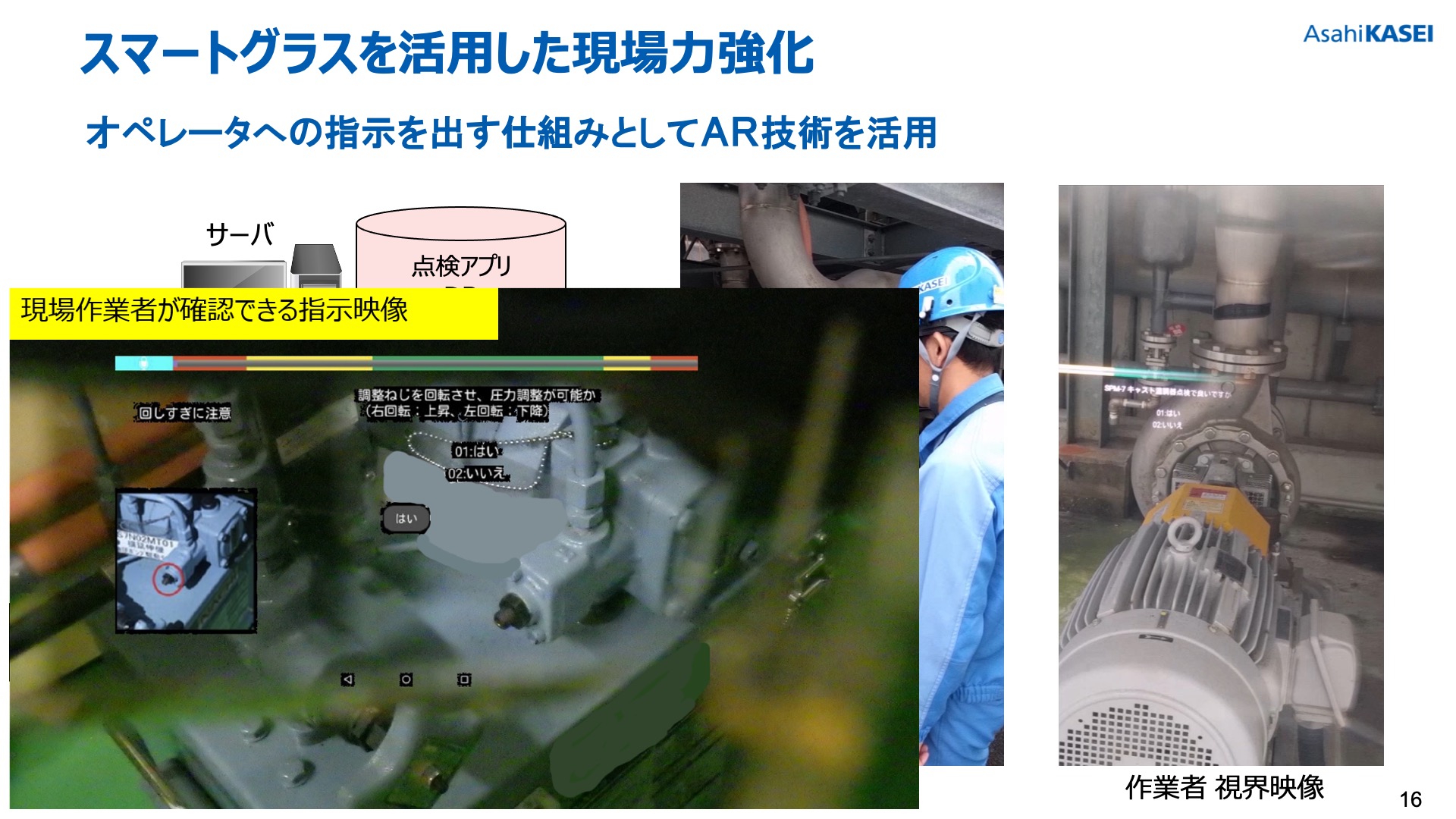
この事例では、スマートグラス上に作業指示が表示され、スマートグラスを装着した現場作業員がその指示を基に実際の作業を行っています。
この取り組みの結果、熟練者のノウハウを継承することに成功しました。
また、コロナ禍において海外への出張が行えないなどの制限の中でも、海外設備の故障時の復旧作業やプラント立ち上げを継続することに貢献しています。日本からスマートグラスを現地に送付、現地作業員がスマートグラスを利用することで、日本からの指示を無事に現地作業員が実行できるようになったのです。
次に、旭化成が持つ水素生産術であるアルカリ水電解システムを用いて実証実験を行っている福島水素エネルギー研究フィールドの事例もご紹介いただきました。
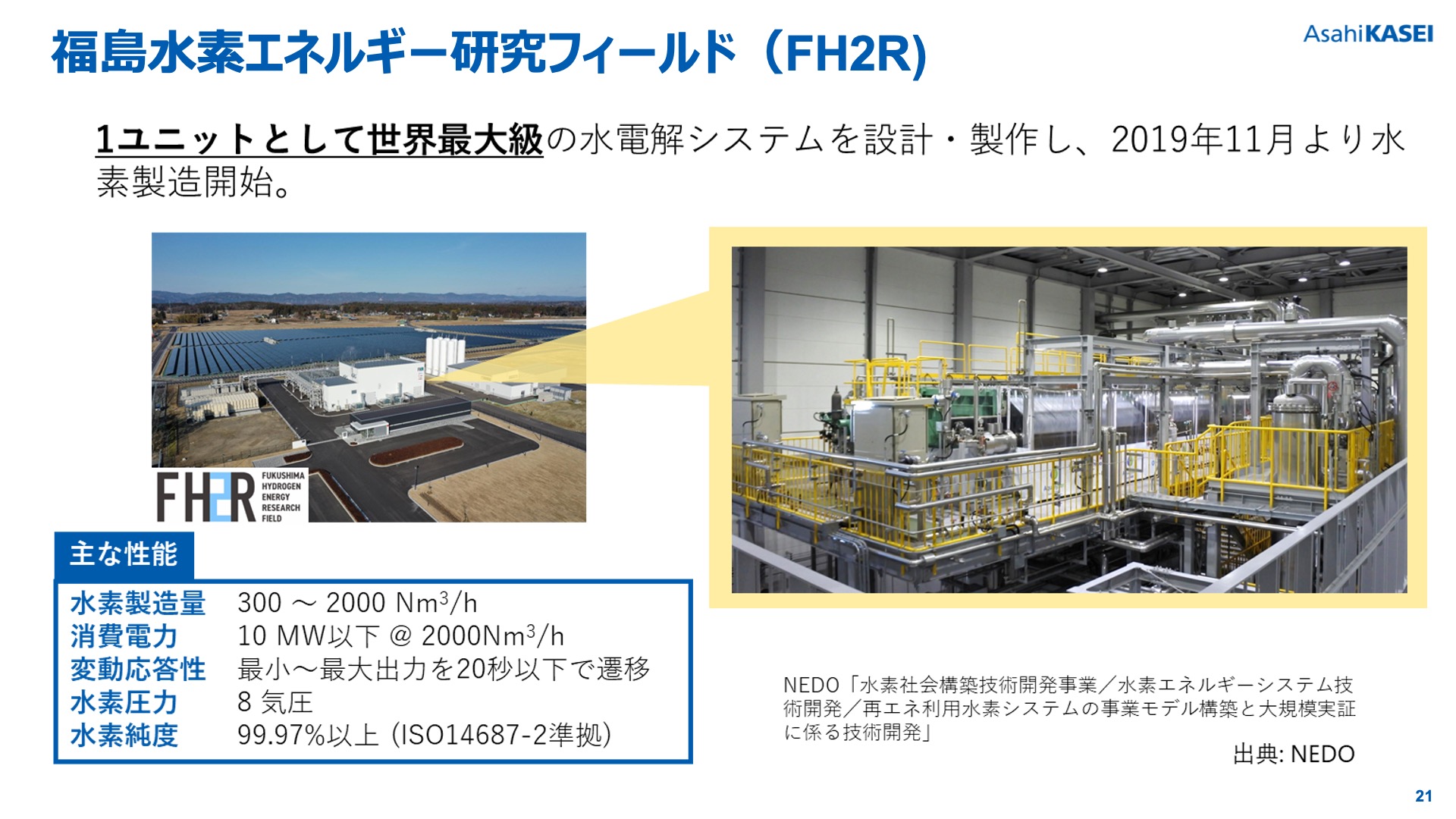
福島水素エネルギーフィールドではデジタルツインを用いた運転・保全作業の高度化への取り組みを行っています。
プラント建設の設計時に利用した3DモデルやP&ID図に加えて、DCS上の実際に稼働しているデータ、そして各種マニュアルや写真の画像データを組み合わせてデジタルツインを作成します。
現場の作業員はウェブアプリケーションやスマホのアプリケーションから作成したデジタルツインへとアクセスします。
その結果、実際の作業中にはすぐにP&ID図やマニュアル、点検履歴、運転データである実績値の確認を行うことができるようになりました。
そして、こちらでもスマートグラスを用いたプラント運転の高度化が今後予定されています。
デジタル活用から学んだDXの推進ポイント
では、実際にDX推進を行い、現場のデジタル化を進めている原田様はDX推進のポイントをどのようにお考えなのでしょうか?
それは下記の3点です。
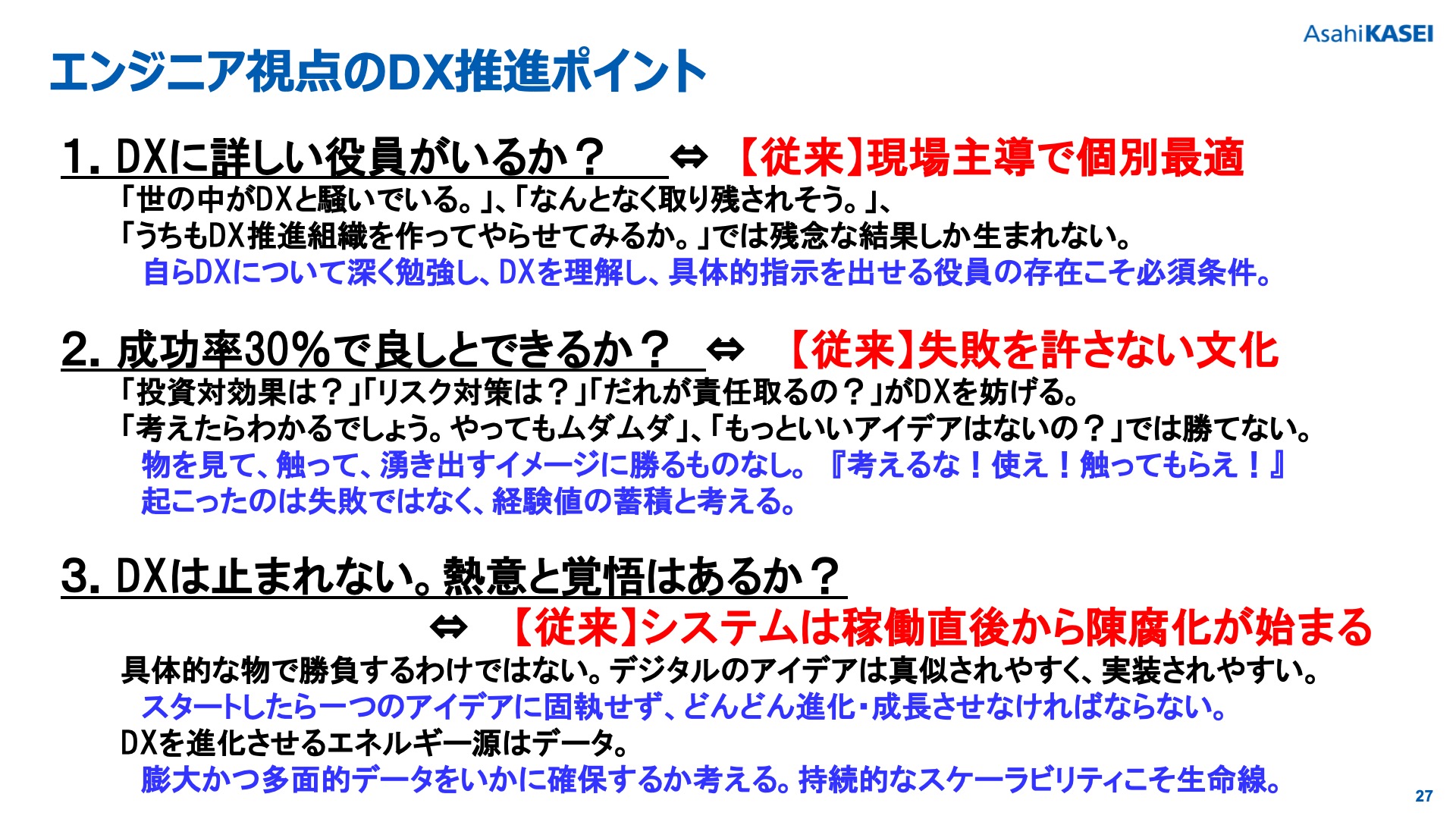
- DXに詳しい役員がいるか?
「役員自身がDXについて学び、実際の担当者にまで指示ができることが必要」と原田様はおっしゃいます。役員レベルの方々が自身で推進しない限り、現場主導でDXが進んでしまい、結局は個別最適しか達成できないのです。 - 成功率30%で良しとするか?
旭化成でも失敗を許すことができないという文化から「投資対効果」や「リスク対策」の説明を求められることが多かったようです。しかし、DXの推進には「物を見て、触ってもらって、そこから湧き出すイメージが重要」とおっしゃいます。うまくいかなかったことはすべて失敗ではなく、経験値の蓄積なのです。 - DXは止まれない。熱意と覚悟はあるか?
「デジタルはどんどん進化させることが重要で、そのエネルギー源はデータ」
DXにて行っている取り組みは見かけ上は真似されやすいものです。しかし、社内の膨大かつ多面的なデータを用いて推進することで、他社に真似されず、進化し続けていくことができるのです。
最後に原田様は「人・データ・組織風土がデジタル変革の成功要因である」とまとめられ、「デジタルの力があれば国や組織、文化を超えてよりよい暮らしや地球に貢献できる」というお言葉で本講演を締めくくりました。