As we discussed in our blog on Generative AI in industrial environments, operators have many new opportunities to improve operations with Generative AI and turnaround (TAR) planning is no exception. TARs are complex processes that involve shutting down production, conducting essential maintenance and repairs, and restarting operations efficiently while minimizing downtime. Currently, half of turnarounds are delayed by 20% or more and over 75% exceed their budget by at least 10%[1].
Applying Generative AI to the turnaround planning process will not only reduce the time and effort to plan turnarounds, but it will also shorten TAR timelines and increase annual production capacity and revenue potential. But given its potential, why is generative AI not yet mainstream in the process? What must be in place to use it successfully to drive change?
Turnaround planning has an industrial data problem.
Successful turnaround execution starts with effective TAR planning, an equally complicated process involving extensive and meticulous planning, scheduling, resource allocation and coordination, logistical challenges, risk management, and more.
Pains of TAR planning
- Long term cycles
- Budget constraints
- Maintenance is preventive, not predictive
- Many stakeholders, limited collaboration
- Afterwards, equipment still fails
Traditional turnaround planning relies on unique, homegrown processes, manual data aggregation from many isolated solutions, and an army of internal and external teams. As a result, there are challenges accessing reliable data and insights, communicating well across teams and contractors, standardizing processes, and harnessing all of the existing data effectively.
While the market offers a multitude of solutions and services to solve isolated use cases within TAR planning, the industry is still struggling to find a comprehensive approach to address these issues. Purchasing a one-size fits all solution is challenging because TAR planning is unique and heavy customization is needed to fit market solutions into existing workflows. With years of domain experience already captured into their processes, each plant/asset has its own constraints, requirements, dependencies, safety protocols, etc..
As a result, plant managers continue to involve a multitude of solutions and rely on humans to perform critical planning tasks. (i.e., scenario analysis, mitigating delays and risks, scope and schedule changes, resource allocation, etc.). Without a more comprehensive, data-first solution, the challenges of the traditional approach (budget overruns, higher costs, limited collaboration, and the inability to leverage data and insights for more efficient TAR planning and execution) will persist.
Read more about the Industrial Data Problem in Asset Performance Management
So where can generative AI make TAR planning less painful and more efficient?
Generative AI can transform the way plant managers are addressing the TAR challenges and processes today by improving failure prediction, optimizing maintenance scheduling and resource allocation, and streamlining and automating manual and paper-based processes. TAR planners can identify the most cost-efficient and productive strategies by quickly comparing various scenarios and considering different constraints and dependencies.
Together, operators and plant managers must explore applying generative AI across the following areas if they want to keep TARs on time and under budget:
Improving communication and collaboration across teams
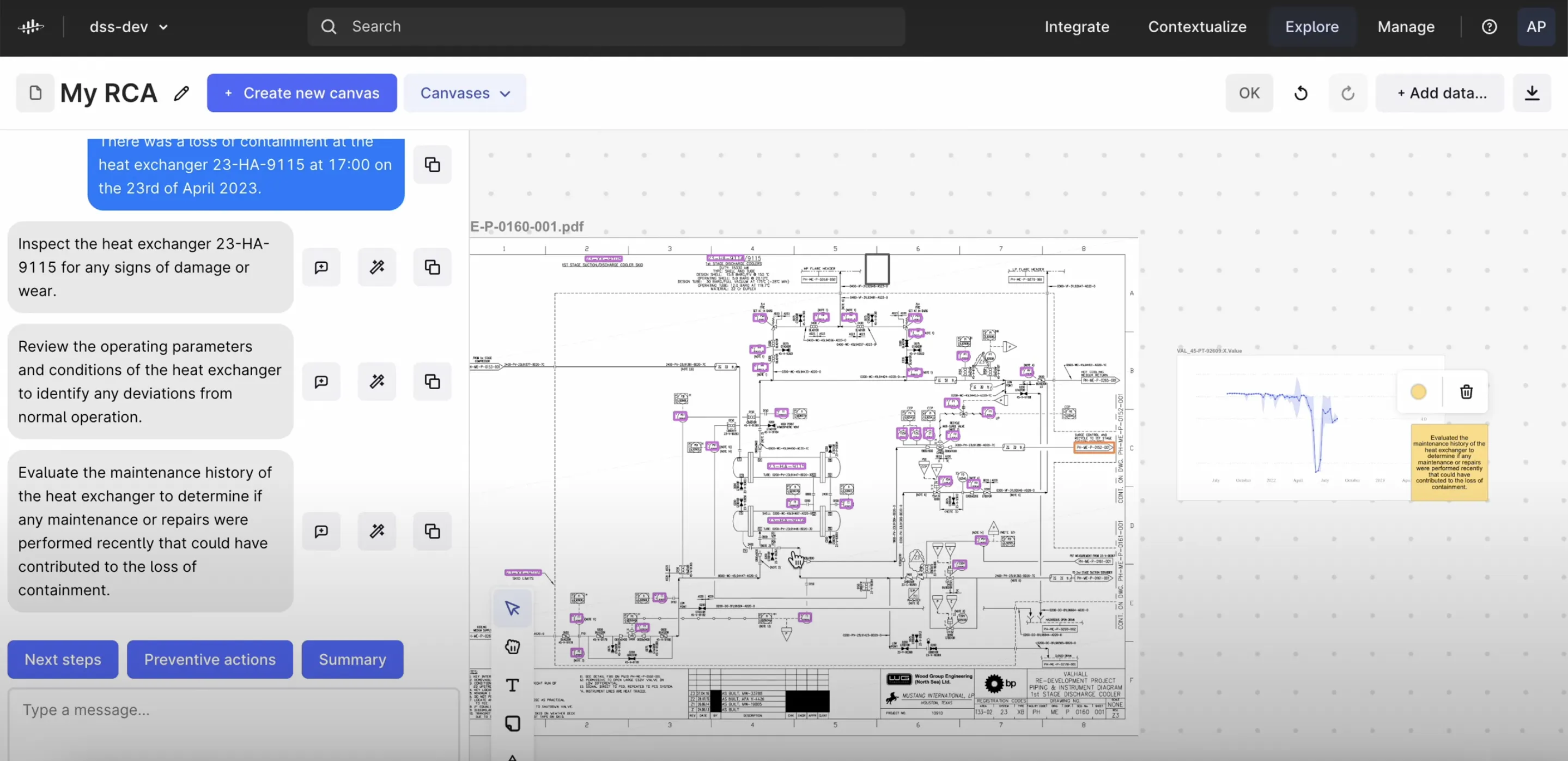
Through sharable workspaces and chat-based interfaces, teams can effortlessly communicate their ideas, share insights, work together on potential bottlenecks, and exchange critical data in real-time. Generative AI can assist in automating repetitive tasks, freeing up time for teams to focus on higher-value activities and fostering a more collaborative and productive environment.
Increasing maintenance predictability
Generative AI algorithms can analyze and process vast volumes of data, including historical turnaround records, sensor data, and maintenance logs. By identifying patterns and correlations within the data, generative AI can provide valuable insights into equipment performance, failure rates, and maintenance requirements. This information lets operators proactively plan maintenance activities, minimizing unplanned shutdowns and outages.
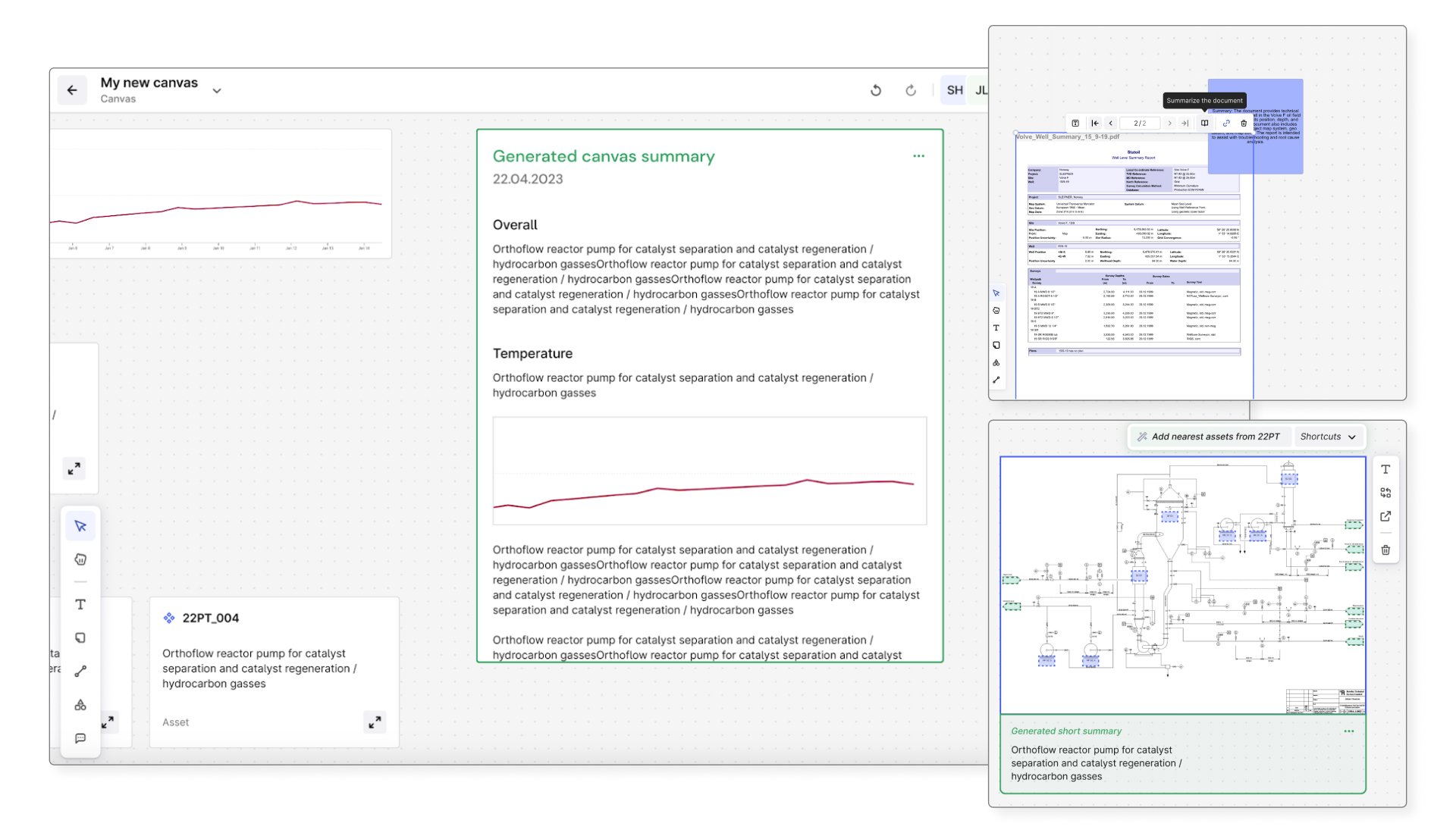
Optimizing scheduling and resource management
Optimize scheduling with generative AI by considering multiple constraints, including resource availability, skill requirements, and interdependencies between tasks. By providing recommendations of ideal schedules, operators can reduce costs, and enhance resource allocation, ultimately leading to more efficient and timely turnarounds.
Safety planning and risk assessment
Assess potential safety risks by analyzing historical incident data, environmental factors, and operational parameters. With Generative AI, simulate various scenarios and generate safety recommendations. By integrating safety planning with turnaround schedules, organizations can proactively mitigate risks and protect workers' well-being.
Continuous improvement
Generative AI can continuously learn and improve from real-time data collected during turnarounds. By analyzing feedback and outcomes, AI algorithms can adapt and refine their models, making future planning iterations more accurate and effective. This iterative improvement process enhances the overall efficiency and reliability of turnaround planning in the long run while simultaneously contributing to the overall health, efficiency, and reliability of a facility or a fleet of assets.
Setting Generative AI up for Success
The successful implementation of Generative AI and ChatGPT-like environments is only possible with a solid data foundation that providesdata in context. Generative AI relies on large volumes of data to learn patterns and generate meaningful outputs, and having high-quality contextualized data provides operators with more accurate prediction scenarios, a reliable overview of equipment conditions and other insights, better resource schedule optimization, and more - all with speed and scale. Failure to operate Generative AI on high-quality data can further complicate TAR (and others), creating more delays, miscalculations, and increased downtime, and, as a result, negatively impact the asset's safety, production KPIs, and overall reliability.
Cognite Data Fusion®is the market leader in building knowledge graphs for industry, and our software can help reduce TAR planning cycles by weeks and months. With our unique automated contextualization engine, industrial organizations can bring more context to their operations in a fraction of the time. For those looking to capture the power of Generative AI for industry, an industrial knowledge graph can prepare your organization to become a first-mover in the opportunities ahead. To apply Generative AI in industrial environments, context means everything.
Sources:
[1] https://www.sciencedirect.com/science/article/pii/S2352484720312622