In late August 2023, Cosmo Oil launched a "digital twin of the refinery" using Cognite Data Fusion®, the leading Industrial DataOps platform from Cognite. With three refineries in Chiba, Yokkaichi, and Sakai, each with its own team of engineers, the digital twin aims to consolidate these refineries into one virtual space in order to enhance efficiency in maintenance operations and increase the productivity of their domain experts across each site.
Beginning in 2019, Cosmo Oil recognized an emerging challenge: the increasing difficulty in hiring new engineers.
According to Mr. Kiyohide Yoshii, Head of Maintenance Strategy and AMP Group at Cosmo Oil’s Engineering Department, there were two primary reasons for this difficulty. The first is the decline in the working-age population due to a decreasing birth rate, a known trend in Japan, where the working-age population is expected to decrease by about 8% by 2030 compared to 2020. This demographic shift made it increasingly challenging to recruit engineers. The second reason is the headwinds facing the petroleum industry. Globally, countries are initiating efforts towards achieving "carbon neutrality by 2050." Consequently, some view the petroleum industry as a declining sector, making new graduate recruitment gradually more difficult.
However, the demand for petrochemical products, particularly, ethylene production, is expected to increase, reaching approximately 33% more than 2018 levels by 2027. Refineries are expected to continue playing a crucial role in the future. Therefore, with demand increasing and the talent pool decreasing, Cosmo Oil anticipated that future refineries would need to be operated more autonomously, with smaller dedicated teams per site.
Approximately 70-80% of an engineer's job involved data collection.
Mr. Yoshii was tasked with finding a way to operate a refinery with fewer engineers. His initial focus was on examining how engineers at the refinery conducted their tasks to see where productivity could be maximized. This investigation revealed a significant realization: "The essence of an engineer's job lies in generating creative ideas. Data is indispensable for this. However, crucial data was scattered in various places, and approximately 70-80% of an engineer's work was devoted to collecting this data," explained Mr. Yoshii.
The term "data" here refers to operational data, maintenance data, inspection records of equipment like heat exchangers and pumps that constitute the refinery, APM (Asset Performance Management) tool data, piping and instrumentation diagrams (P&ID), and data sheets for various components. These were managed in formats such as Excel files, PDFs, text files, printed papers, and filed documents—essentially, they were "siloed."
Without resolving the siloed data issue, it was impossible to enhance engineers' productivity. This led Mr. Yoshii to focus on the concept of "Digital Twin," which was gaining attention in various industries, including the IT sector, during the time of his investigation in the spring of 2022.
The data construction is incredibly fast.
A Digital Twin is a technology that utilizes data collected from the real world, such as plants or devices, to recreate a virtual representation as if it were a twin in the virtual space. At this point, Mr. Yoshii had an image in his mind: "An engineer wearing VR goggles enters the virtual space, touches heat exchangers or pumps, and sequentially checks the associated data."
But how can Cosmo Oil bring this vision to life? Mr. Yoshii’s next step was to find the best data solutionfor the manufacturing industry. A recommendation from an engineering company that "Cognite Data Fusion® has a good reputation” led Mr. Yoshii to test the Industrial DataOps and AI platform out for himself.
Mr. Yoshii’s first impression of Cognite Data Fusion® was that the process of data collection and contextualization, crucial for constructing data, was exceptionally fast.
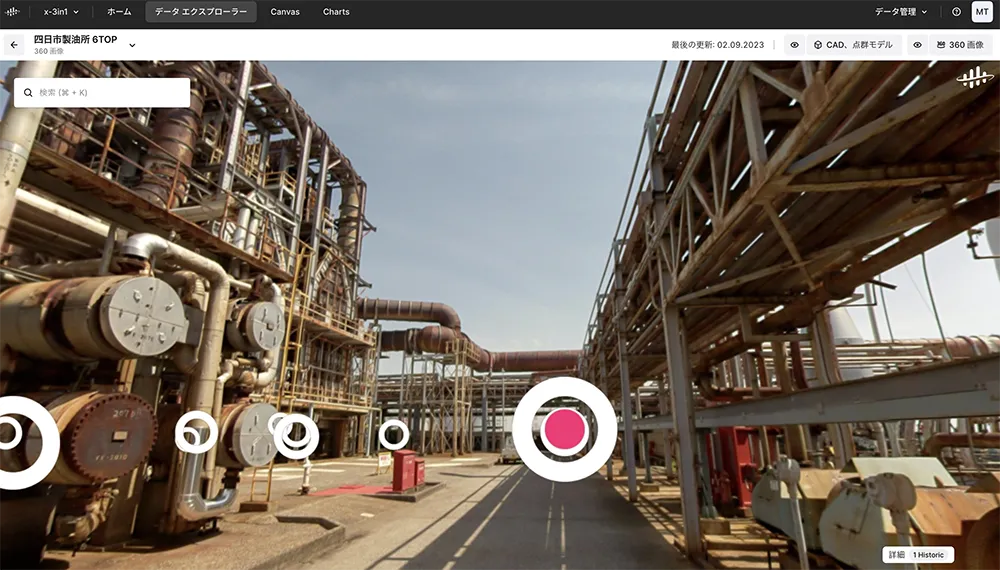
Cognite Data Fusion® has an "AI-OCR feature" that automatically recognizes and tags data, allowing for the swift execution of data construction. Mr. Yoshii explained, "I examined tools from other companies but found that data construction took an exceptionally long time. The goal is to enhance the productivity of engineers, and I determined that spending a significant amount of time on data construction would be counterproductive."
Subsequently, Mr. Yoshii took steps to formally recommend Cognite Data Fusion®.. At the same time, the Cosmo Energy Group held the CDO (Chief Digital Officer) Cup, a competition for digital initiatives. Mr. Yoshii entered his idea to build digital twins for the three refineries using Cognite Data Fusion®. While he didn't win the award, a related company, Maruzen Petrochemical, received recognition for a similar idea that was also powered by Cognite Data Fusion®. "My approach and Maruzen Petrochemical's idea were slightly different. Maruzen Petrochemical's idea was a small-start approach, and that was highly praised," said Mr. Yoshii. In any case, the evaluation of Cognite Data Fusion® significantly increased within the Cosmo Energy Group.
Enabling collaborative maintenance.
The Proof of Concept (PoC) for the full-scale implementation of Cognite Data Fusion® began in April 2023. Initially planned to run until the end of November of the same year, but ended early inAugust because the astonishing speed at which data construction tasks could be executed was quickly apparent. According to Mr. Yoshii, "The speed was such that if we input data in the evening, the data construction task would be completed by the next morning." There was no need for further validation. The decision was made to implement Cognite Data Fusion® in the three refineries.
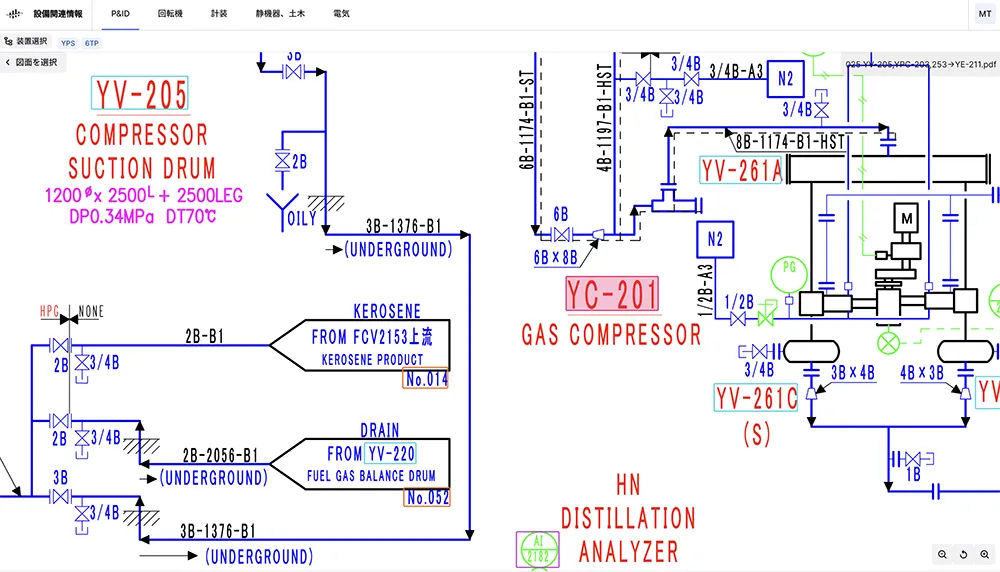
The use of Cognite Data Fusion® in building a Digital Twin enables the realization of "Collaborative Maintenance." "By consolidating the three refineries into one virtual space, we can obtain data from Sakai, Chiba, and Yokkaichi, all from the Tokyo headquarters. This allows us to support maintenance operations for all refineries while in Tokyo or enable engineers from Chiba and Yokkaichi to collaborate on troubleshooting in Sakai," explained Mr. Yoshii. In other words, this leads to increased efficiencies , improvement in working conditions, and maximized productivity across their engineering teams. However, that's not all. Mr. Yoshii sees the potential for future revenue improvement in refineries by combining AI technology with the Digital Twin built using Cognite Data Fusion®.
With the initial success of Cognite Data Fusion®, there are plans to expand the partnership between Cosmo Oil and Cognite. Cosmo Oil is already considering the introduction of "Cognite InRobot" to utilize robots in on-site inspection work.