This article was originally published in Hart Energy.
Industrial DataOps is about breaking down silos and optimizing the broad availability and usability of industrial data—and it’s absolutely crucial for the adoption of industrial robotics.
Robots can increase productivity and safety as well as remove the repetitiveness and tediousness of many of the tasks workers do every day in the industry. These and other benefits have been on full display during the coronavirus pandemic, which has thrown the importance of being able to run operations remotely into sharp relief.
The development of robotics systems has reached a tipping point. Robots are capable and secure enough to work in industrial settings and affordable to the point where the economics of automating certain workflows make sense.
This development couldn’t have come at a better time. Asset-heavy industries (e.g., oil and gas, power and utilities, and manufacturing) are facing growing pressure to produce more to meet the world’s growing demands for energy and goods while cutting costs, emissions and waste.
Hardware alone isn’t enough to meet these challenges. Without the right industrial software, a robot is just another siloed system. To incorporate robots into a digital transformation strategy, industrial companies need to collect and connect the valuable data gathered by robots, contextualize it with other existing data from IT, OT and ET systems, and make the data available and understandable to the growing list of data consumers (i.e., control room operators, field workers, data scientists, solution engineers and more).
Robots need Industrial DataOps
This type of cross-organizational data management is called industrial data operations (DataOps). Industrial DataOps is a specific approach to handling data, and it is necessary if industrial companies want to move toward an autonomous future.
Industrial DataOps in the 2020s is as new and unknown as DevOps was in the 2010s, as business intelligence was in the 1990s and as human resources was in the 1890s. Put simply, Industrial DataOps is about breaking down silos and optimizing the broad availability and usability of industrial data—and it’s absolutely crucial for the adoption of industrial robotics.
Since Industrial DataOps is about making data available and meaningful, its uses are varied. Examples in asset-heavy industries include maintenance workflow optimization, engineering scenario analysis, and digitization of asset process and instrumentation diagrams to make them interactive and shareable.
Industrial DataOps also enables oil and gas companies to build 3D digital twins, which is particularly important to industrial robotics. Robots can navigate industrial facilities based on data in digital twins, and the data they capture keep the digital twins updated. This close connection between hardware and software adds human-like meaning and association to the thousands of images, sensor readings and other data.
In other words, the industry needs Industrial DataOps to enable robots to conduct autonomous remote missions, but we also need Industrial DataOps to make sense of the information that comes back from these missions.
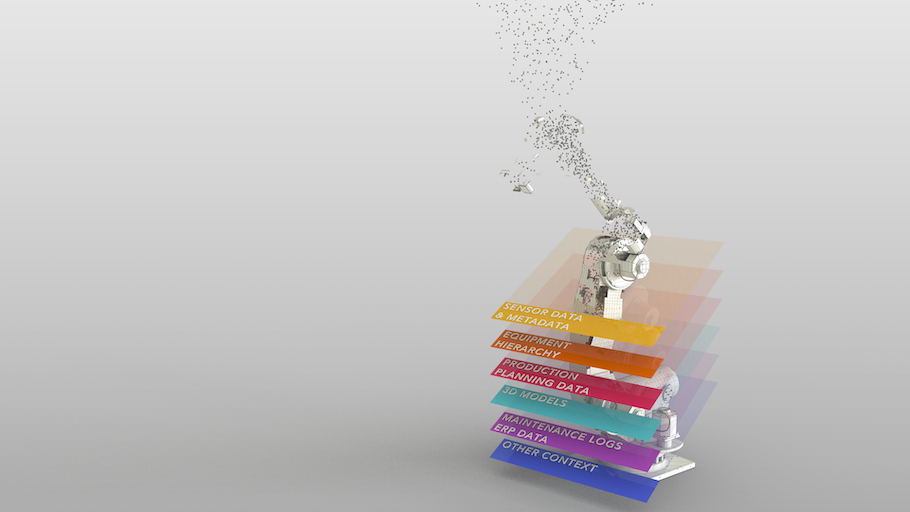
Industrial robotics only work when organizations understand the value of collecting and connecting data, contextualizing it and making those data both available and understandable.
Industrial robotics in action
Cognite, a global industrial software-as-a-service (SaaS) company, has worked with asset-heavy industries around the world for years to digitalize their operations. Cognite Data Fusion®, Cognite’s Industrial DataOps platform, serves as the foundation for automation and robotics data contextualization for companies in industries such as oil and gas, power and utilities, manufacturing and shipping.
Spot goes offshore in the North Sea
In 2020 Cognite and the independent European E&P company Aker BP partnered to pioneer remote-controlled offshore missions on the Skarv installation, an FPSO unit located 210 km offshore in the North Sea. The project featured Spot, the four-legged robot dog developed by Boston Dynamics.
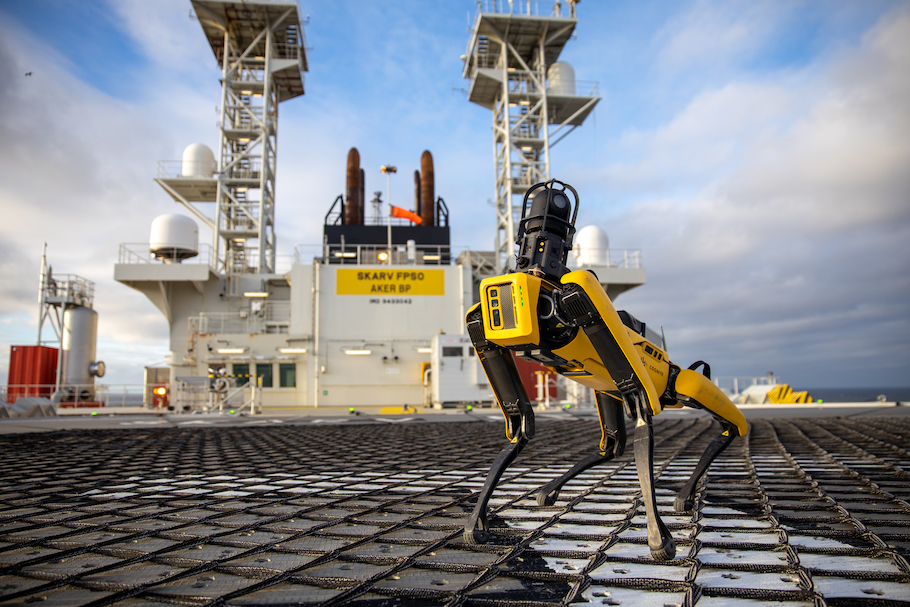
Spot, remotely controlled from a home office onshore, performs autonomous inspection.
Spot was verified and tested for both offshore mobility and communications. Over the course of a week, Spot was remotely controlled from a home office onshore. Tasks included autonomous inspection, high-quality data capture and automatic report generation.
The deployment was an important step toward greater use of robots in the oil and gas industry, showing how robots can handle inspections rounds, night shifts and other repetitive tasks. Remote operations with robots can reduce costs and give operators more time for in-depth tasks, making offshore operations safer, more efficient and more sustainable.
Autonomous inspection of remote facilities
Cognite worked with a major Norwegian grid operator to incorporate robots into its inspection workflows for remote sites to reduce its climate gas emissions, ensure higher uptime through data-driven maintenance and keep people out of harm's way.
Spot was deployed at an indoor substation, ingesting images, sensor readings and other data to generate 3D models and create an operational digital twin of the facility—all in just two days.
After a quick tutorial, anyone in the organization can remotely deploy complex, autonomous inspection missions that combine ground-based robots and flying drones for multiple asset inspection across multiple locations.
The grid operator has set an ambitious goal of cutting its climate gas emissions by 25% by 2025. An internal analysis found that robots are a cost-effective way of remotely reading analog gauges and monitoring gas levels at remote facilities, which will help the grid operator reach its emissions target.
Using robots to maintain the accuracy of a digital twin
Cognite worked with an engineering company that provides integrated solutions, products and services to the global energy industry to create a digital twin of one of the company’s 173-acre construction yards. The digital twin creates a virtual representation of the physical reality at the construction yard, providing regularly updated location information about key items and enabling users to quickly locate what they need.
Data collection via robots and other devices keeps the information in the digital twin current without increasing the workload of employees at the yard. With up-to-date information about materials, vehicles, equipment and more at their fingertips, all 3,000 employees at the site can make data-driven operational decisions that reduce costs and risk in building projects (e.g., improving logistics with vehicle tracking and using drone scans for precise measurements of the yard).
An independent consulting firm has estimated that maintaining an overview of all assets, tools and equipment used in a typical topside project generates about $.27 per pound in savings. For large projects, this adds up to millions of dollars in savings.
Robots can help industrial workers be in more places at once, track more changes over time and use more data in their decision-making processes. This will require software that gets data to experts in a form they can understand and act on.
Consistent across all the examples above is the value of collecting and connecting data, contextualizing it and making those data both available and understandable. This is Industrial DataOps, and it’s the future of industrial data management and industrial robotics.