Picture this scenario:
A building materials company has just produced a fresh batch of cement. To test the quality of the cement, the company then produces a concrete element. Weeks later, once the concrete has hardened, the quality control turns up an issue. The cement wasn’t up to standard.
Why wasn’t the issue detected earlier? In this scenario, there wasn’t a live sensor that could predict the quality of the finished product early on in the production process. But even in the cases where sensors do exist, they sometimes stop working — or are never installed in the first place.
The manufacturing industry has a sensor problem. To fix it, we need to look at how other heavy-asset industries use machine learning and root cause analysis to produce data-driven predictions that manufacturers can act on with confidence to optimize production and reduce waste.
Lessons from the Oil and Gas Industry
The oil and gas industry has embraced the use of soft sensors, sometimes called virtual sensors. A soft sensor is a model that can predict a property indirectly by looking at other available sensors. In some situations the soft sensor can be a pure mathematical model, like computing fluid density by combining pressure and temperature measurements, information about the composition of the fluid, and the laws of thermodynamics. Such a soft sensor will give real-time predictions of the quality of the product, notifying operators and enabling them to perform mitigating actions before it’s too late.
Some phenomena are too complex to be modeled using pure mathematical models. This is where machine learning can fill the gap.

In these cases, the spot samples serve as our training data, telling us about the outcome of a certain combination of sensor values.
Even in cases where we can’t model the complete process using physics models, we can model subcomponents and input the results into a machine learning model. This is often called a Hybrid AI model, or Physics-Guided ML. This isn’t a mandatory step, but it is a way of improving the accuracy and reliability of a model.
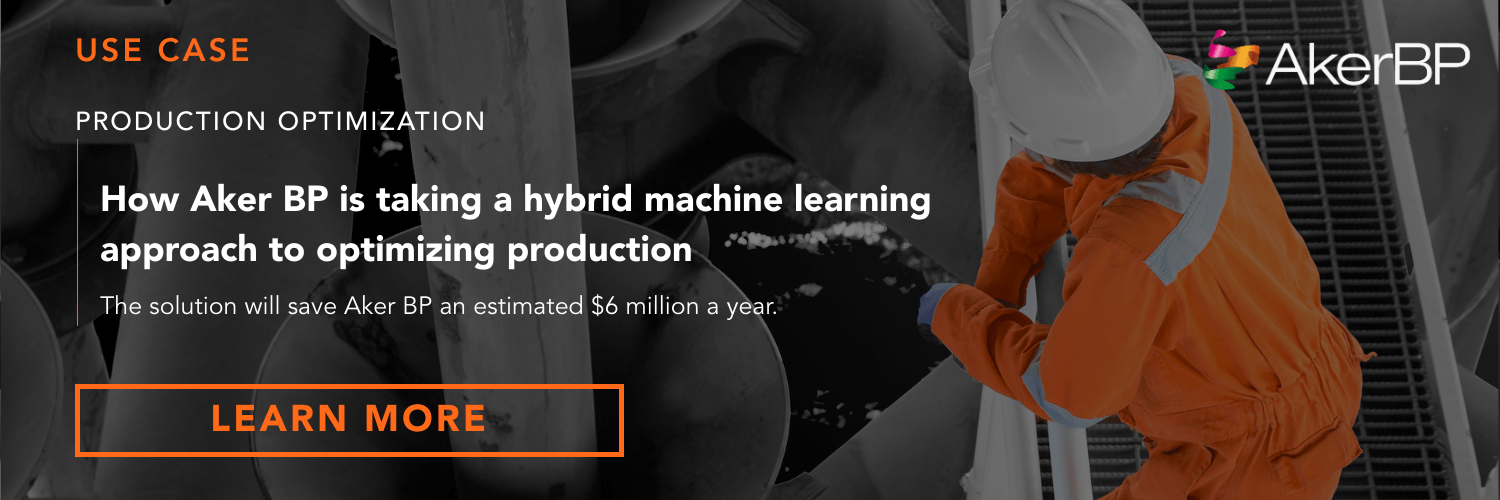
Predicting whether or not the quality of a product will be up to standard is just the first step, however. We also need to predict why. This is called an automated root cause analysis (RCA). The RCA information is pulled from a similar model as the soft sensor, giving the manufacturer an indication of where in the process there is a problem and enabling them to troubleshoot more efficiently.
Finally, we need to predict how we can mitigate issues. Even though a manufacturer knows what the problem is, they rarely have the opportunity to directly influence a single parameter without disrupting several others. There is usually a limited number of control parameters and a limited parameter range.
This method will optimize on the control parameters inside of the allowed parameter range to recommend mitigating actions that reduce the problem, for example increasing the quality parameter to above a predetermined threshold.
Read also: The top digitalization trends and opportunities changing the manufacturing industry
Different Phenomena, Same Solution
Even though the manufacturing industry deals with its own processes and phenomena, we can tackle production optimization challenges by applying strategies and lessons from the oil and gas industry.
At Cognite, we’ve worked with digital frontrunners in the oil and gas industry, including Aker BP, OMV, and Wintershall Dea, to optimize processes and make their operations faster, safer, and more sustainable. We’ve codified all that experience into Cognite Data Fusion® (CDF) to help manufacturers draw insights from their data and unlock opportunities in real time.
Learn more: Cognite’s Industry Solutions for the Manufacturing Industry
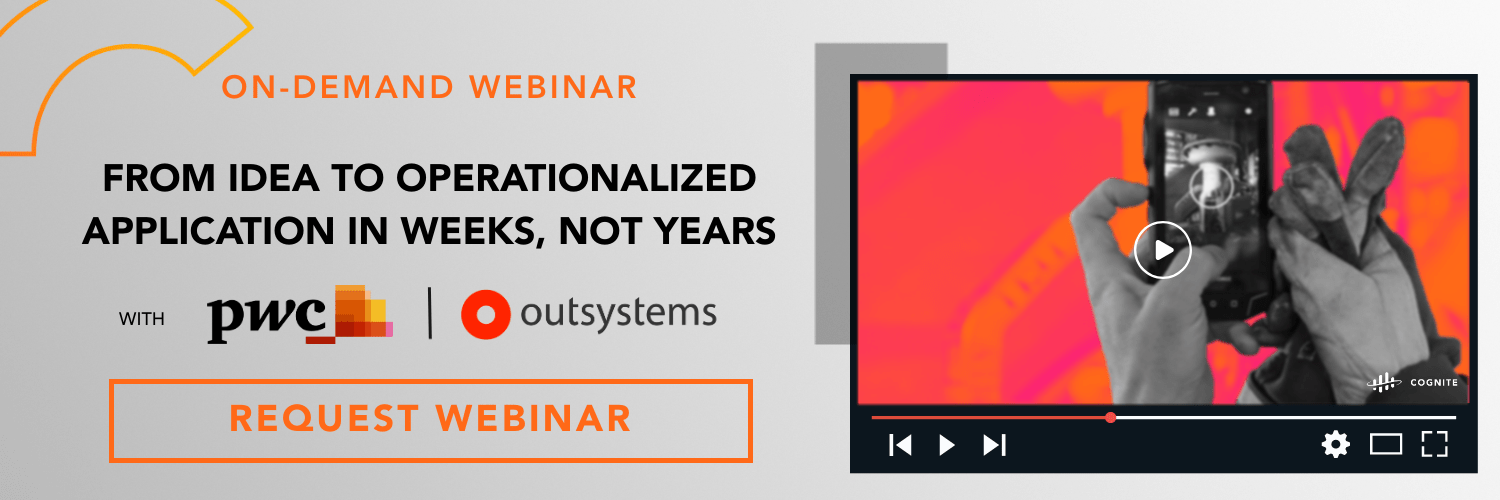