Manufacturing companies face an uncertain business environment filled with trade conflicts, fluctuating raw material costs, and evolving consumer demands. This uncertainty is driving business leaders to look inward, where investments in information and operational technologies could bolster their bottom lines.
Intelligent, interconnected, and automated factories allow manufacturers to scale and adapt capabilities as they seize new opportunities and respond to changing demands. In this way, new digital technologies deliver tangible solutions for manufacturers facing unpredictable market realities.
We took a closer look at the top digitalization trends changing the manufacturing industry. We discovered not only how these technologies transform manufacturing, but how they fit into a workforce management model that future-proofs manufacturing environments and drives long-term business value as well.
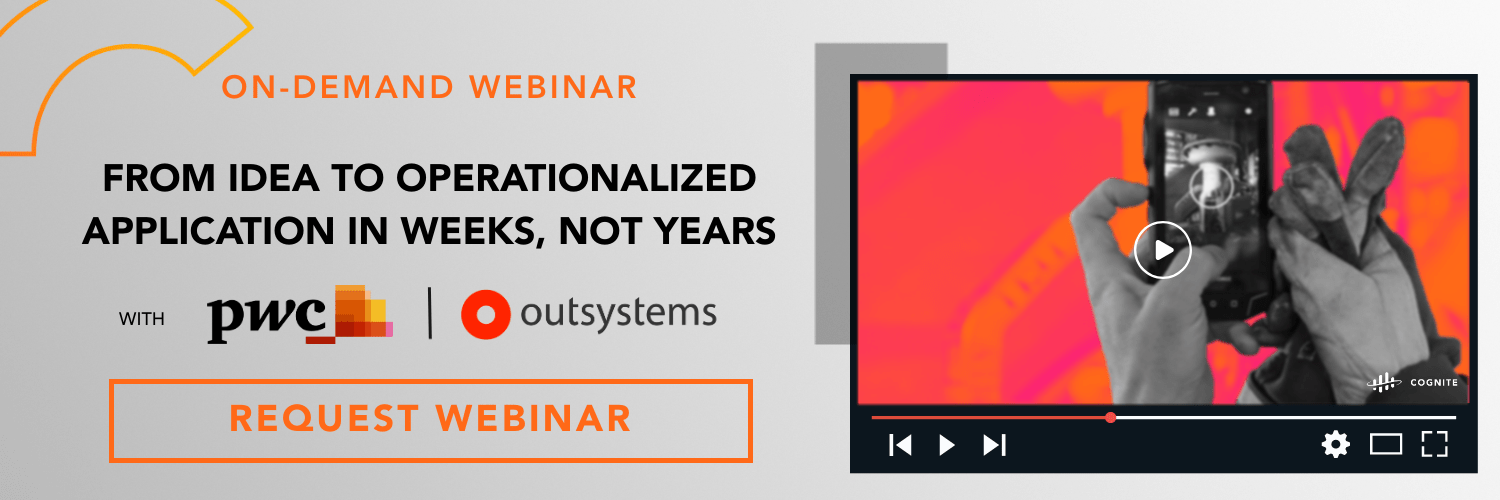
Digitalization Trends and Opportunities in Manufacturing
Modern manufacturing is about realizing possibilities through technology — and while half of manufacturers are piloting or implementing new technology investments, roughly one-third are still “knowledge gathering, investigating, and developing their strategies,” Gartner reports.
But few companies can afford to wait on business-critical investments if they want to remain competitive. Modernizing production systems is critical as digital technologies reshape the manufacturing sector and drive game-changing performance improvements among early adopters.
Forward-looking manufacturers are pursuing next-generation digital tools, including artificial intelligence (AI) and Internet of Things (IoT) sensors that are changing competitive dynamics in their fields. They will look to optimize the way information technology (IT) and operational technology (OT) investments work together to produce business value. Connected technologies will strengthen the links between OEMs and other segments of their supply chains — including end customers — as well.
Read also: Clean up your data lakes: Data contextualization in the manufacturing industry
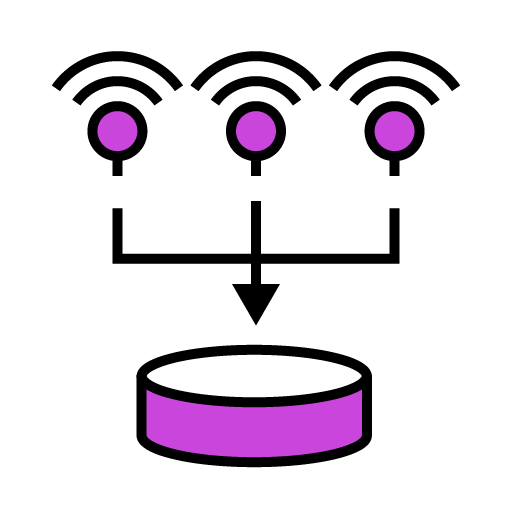
Opportunity No. 1: Connecting IT and OT infrastructure with Internet of Things (IoT) sensors
IoT technologies are proliferating among manufacturers as real-time dataflow and analysis revolutionize productivity, ROI, and preventative maintenance. Nearly 70% of manufacturers credit IoT with profit growth; manufacturers will have invested $267 billion in IoT technologies by 2020, Forbes reports.
IoT will only grow in its importance as it converges with AI and other cognitive systems, “improving performance transparency and access to real-time information through more user-friendly visualization for operators and managers,” as McKinsey describes. Use of IoT will continue to expand in the 2020s as manufacturers find more operational applications, effectively spanning the gap between their IT and OT investments.
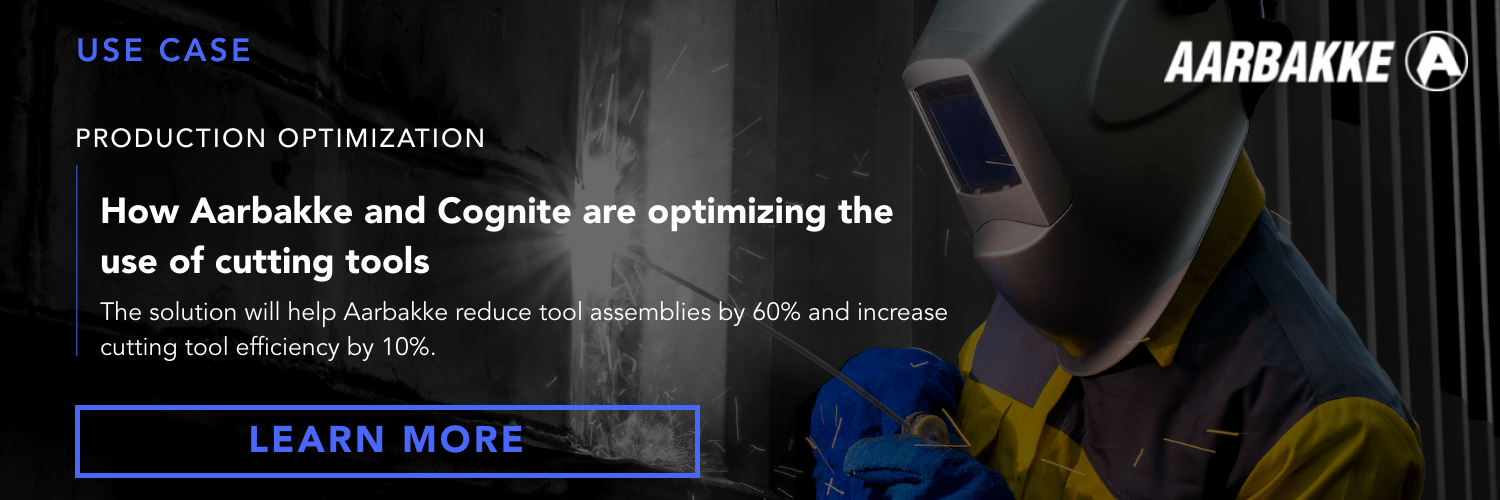
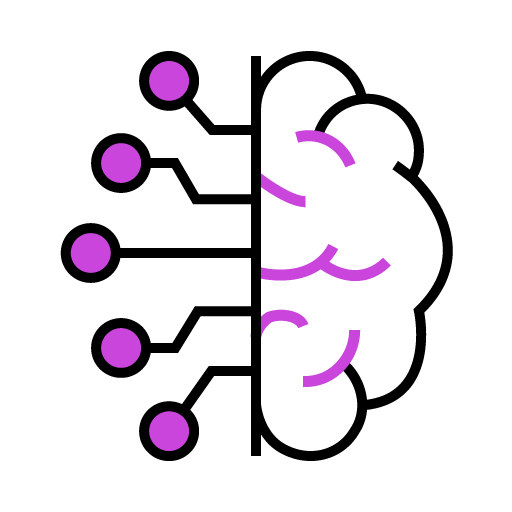
Opportunity No. 2: Boosting value, productivity, and cost savings with artificial intelligence
Thinking machines are rapidly evolving, allowing manufacturers and their partners to build, train, and test neural networks with applications across verticals and departments. Analysts at McKinsey believe that manufacturers that implement AI now can expect a 122% increase in cash flow over the next five to seven years — companies that do not can expect only 10% growth.
Predictive analytics is perhaps one of the most critical AI applications in manufacturing. Intelligent predictive models allow manufacturers to consistently prevent the downtime once common to the industry — where a single hour of downtime can equate to $100,000 in losses in a manufacturing environment, according to Forbes: “Using data, AI, and predictive analytics, some say manufacturers can reduce planned outages by 50%.”
But AI has dozens of operational applications as well. German manufacturer Bosch uses automated tools to support workers managing its internal operations — from procurement to shipment logistics. They anticipated €1 billion (US$1.13 billion) in cost savings from this effort by 2020, PwC reports. The application of machine learning to manual and mechanical processes dramatically reduces the need for human intervention, boosting productivity and freeing human workers to add value in other ways. Manufacturers will find even more applications for AI as it enhances capabilities within other digital systems.
.png?width=71&name=Icons%20Updated-91%20(1).png)
Opportunity No. 3: Optimizing the digital workforce to unleash subject-matter expertise
McKinsey estimates that between $1.2 and $3.7 trillion in global productivity gains are “up for grabs” in the manufacturing sector by 2025. Manufacturers who stay ahead of the curve on evolving digital technologies — and find applications that add value at scale — are best equipped to achieve a long-term competitive edge.
But as technologies evolve, workforces must evolve with them. Even though an estimated 60% of today’s manufacturing jobs could in theory be automated with available technology, the transition will take decades — and companies will still need skilled people to manage, maintain, and use those digital technologies successfully when those transitions are complete.
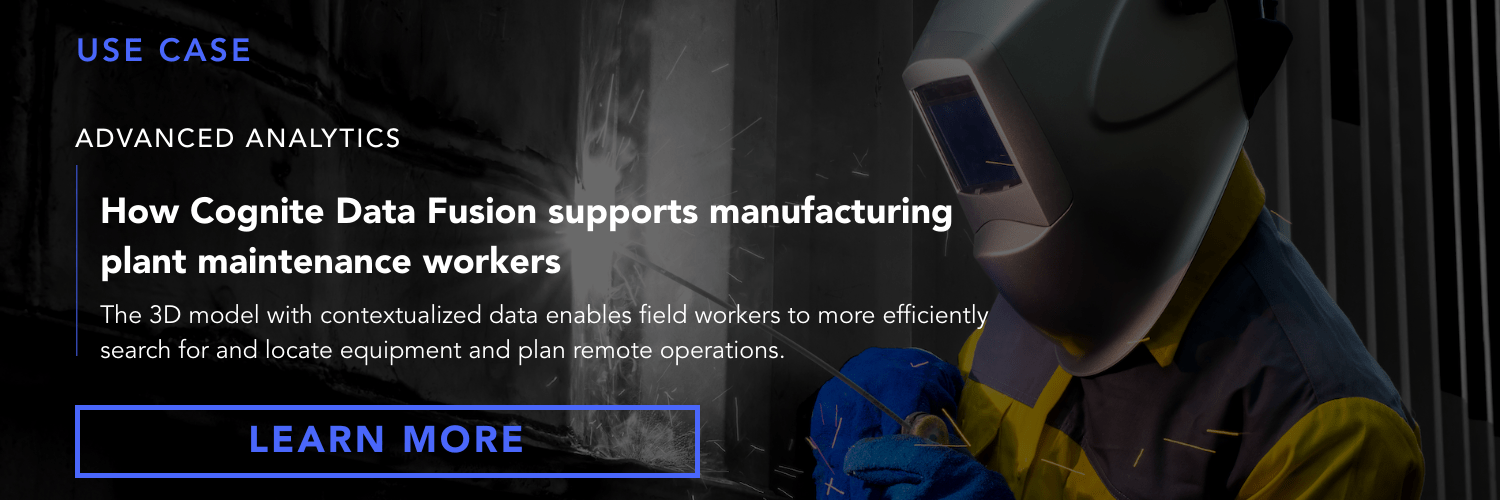
Act now on the digitalization trends reshaping the industry
2020 has been a volatile year for heavy-asset industries. The oil and gas industry, for example, was still feeling the aftereffects of the crash of 2014. Then came the novel coronavirus pandemic. All of a sudden, companies that had been planning to grow found themselves searching for places to cut.
So far, there is one line item that companies aren’t touching: digitalization. Now more than ever, forward-looking manufacturers are investing in the skills and technologies that will help them optimize their products and reduce waste, including digital solutions that enable remote monitoring and diagnostics of equipment in the field, self-service condition monitoring, and secure data sharing between themselves and customers.
It’s time for manufacturers to take a critical look at their own capabilities and determine whether or not they’re set up for success in a rapidly changing industrial landscape. You can do so by asking yourself a handful of questions:
Is your data locked away? If your engineers are spending more time searching for data than they are analyzing it, your time to value will get significantly longer. Start by breaking down the silos and collecting all the data you produce in a single location.
Is your data contextualized? If you’re unable to combine insights from different data sources — maintenance data, events from the CMMS, control system data, and sensor values, as well as use physics and reliability models to describe the expected behavior of equipment — your solutions likely won’t be able to accurately predict failures and suggest timely, targeted maintenance actions.
Is your data shareable? Making data available across your organization is only the first step. Transforming heavy-asset industries will take ecosystems of operators, manufacturers, and others, all committed to sharing high-quality data securely.
Volatile times shouldn’t preclude change. In fact, the time for fundamental change in the industry is now. The companies that are investing in digital transformation now are laying a foundation that will make the industry smarter, more efficient, and less wasteful.
This post is an excerpt from the white paper Intelligent Factories: The Data-Driven Future of the Manufacturing Industry.
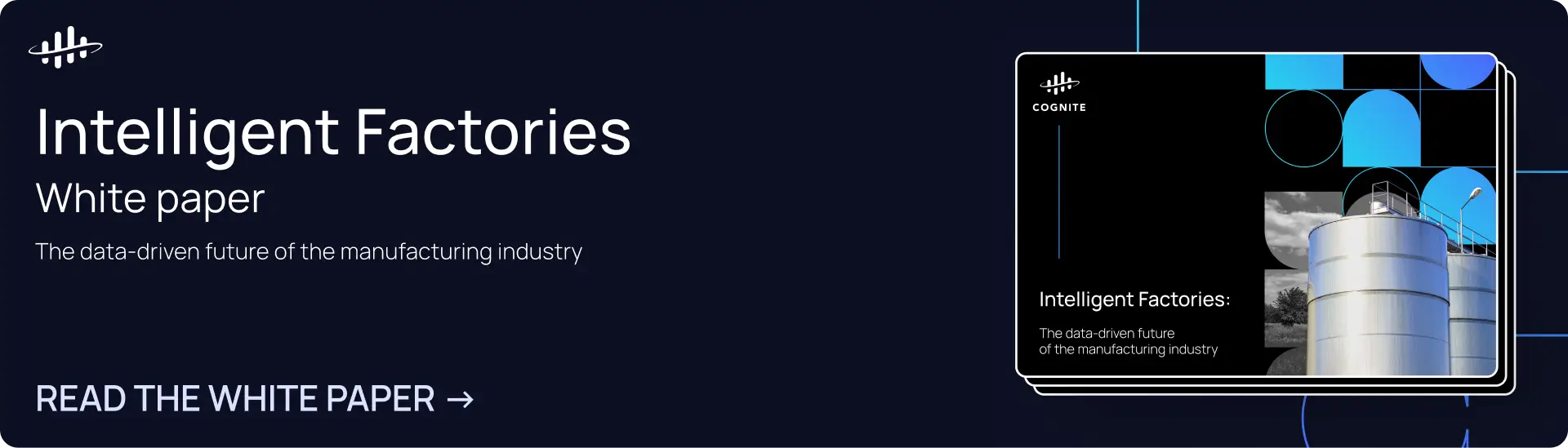